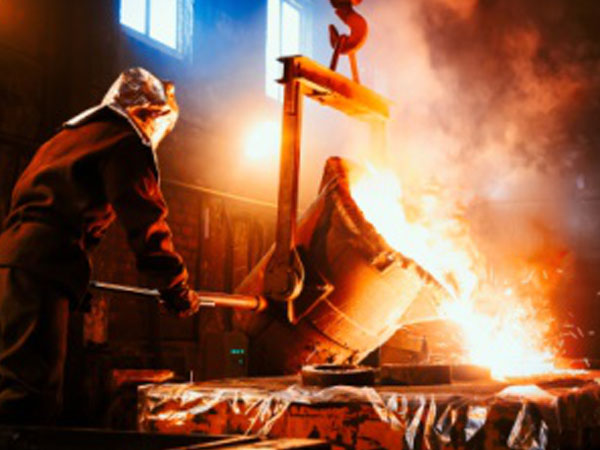
Foundry Melting Shop Equipment List
Generated by the electromagnetic induction. This eddy current generates Joule heating, and a heat loss of the electromagnetic energy (eddy-current loss) will be caused. High frequency induction heating equipment performs heating by utilizing the two heating principle, namely hysteresis loss and eddy-current loss.
Ladle and PRE Heaters
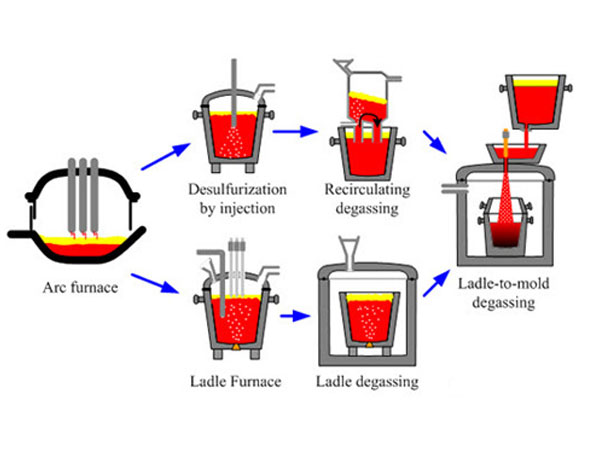
Ladle furnace is a kind of refining technology outside the furnace by arc heating under vacuum conditions. It is mainly used to refine molten steel melted in primary furnaces (electric arc furnace, open hearth furnace and converter), and can adjust molten steel temperature and process buffer to meet the requirements of important metallurgical equipment for continuous casting and rolling. Ladle furnace is one of the main equipment for refining outside the furnace.
Main functions of ladle furnace:
1. Molten steel heating and insulation function. New heat energy is obtained from molten steel by electric arc heating, which can not only add alloy and adjust composition during ladle refining, but also add slag to facilitate deep desulfurization and deoxidation of molten steel. In addition, the opening temperature of molten steel required for continuous casting is ensured, which is conducive to the improvement of dry slab quality.
2. argon stirring function. Argon is blown into the molten steel through the permeable brick installed at the bottom of the ladle, so that the molten steel can obtain a certain stirring effect.
3. Vacuum degassing function. After the ladle is hoisted into the vacuum tank, the steam jet pump is used for vacuum degassing, and the molten steel is blown with argon at the bottom of the ladle for stirring, which can remove the hydrogen and nitrogen in the molten steel and further reduce the oxygen content and sulfur content. Finally, higher purity molten steel and materials with superior performance are obtained. For the whole enterprise, the application of ladle furnace can at least increase the following benefits: speed up the production pace and improve the overall metallurgical production efficiency. Application: ladle furnace is widely used in industry, steel, metallurgy and other industries.
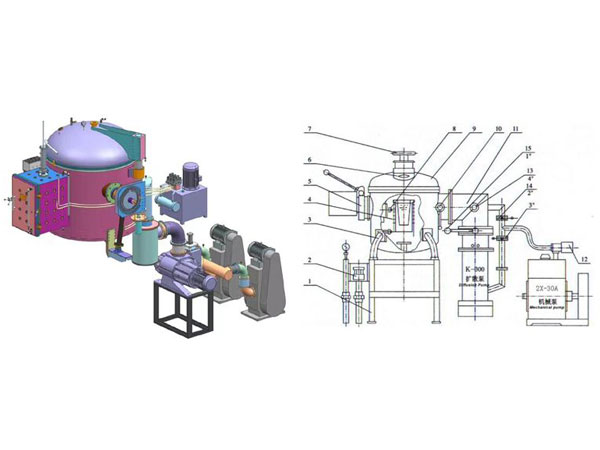
Vaccum Melting
Vacuum Induction melting offers an attractive combination of a controlled atmosphere (vacuum or inert gas) and precise control on the melting process
A solid state RF power supply sends an AC current through a water cooled copper coil and a metallic charge is placed in a ceramic (or graphite) crucible inside the coil. The coil serves as the transformer primary and the part to be heated becomes a short circuit secondary. The metals placed within the induction coil feels a varying magnetic field and circulating eddy currents are induced within the metals. Flow of eddy currents leads to resistive heating of the metals; further leading to their melting without direct contact between the crucible and the coil. Depending on the inductive coupling of the coil with the charge materials, the induction furnace can go to a temperature of 1800ºC or more. About 100 g of metals can be melted at a time.
Induction Melting Furnace
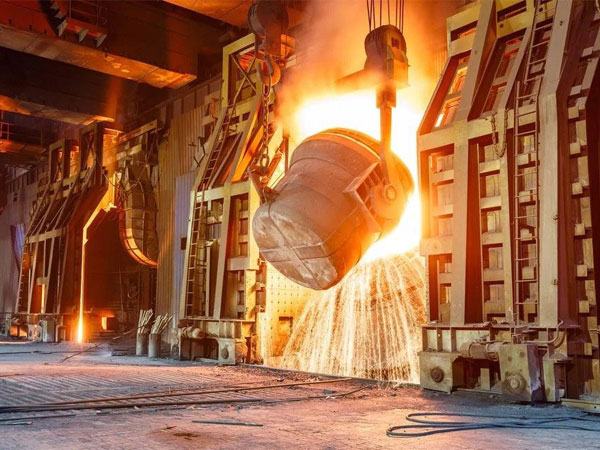
Induction furnace is a type of furnace for steelmaking which uses electrical energy for its operation. Induction furnace (IF) steelmaking is one of the two electrical steelmaking processes. The other process for electrical steelmaking uses an electric arc furnace (EAF). Though IFs are being used since a long time, the production of mild steel by the IF is relatively not very old phenomenon.
The principle of melting in IF is that a high voltage electrical source from a primary coil induces a low voltage, high current in the metal or secondary coil. IF uses the heat produced by the eddy currents generated by a high frequency alternating field. The alternating magnetic field produced by the high frequency current induces powerful eddy currents in the charge resulting in very fast heating.
Gleam Business provides all kinds of solution for a complete setting up of induction furnace throughout the world. Induction heater units incorporate high frequency generators for non-contact heating of metal using electromagnetic induction. When AC is applied to a coil surrounding the work (metal), a magnetic field is generated by the current flowing in the coil, and induced loss (hysteresis loss) is generated causing a heat. At the same time, in the magnetic field which alternates with the AC, a spiral current (eddy current) is generated by the electromagnetic induction. This eddy current generates Joule heating, and a heat loss of the electromagnetic energy (eddy-current loss) will be caused. High frequency induction heating equipment performs heating by utilizing the two heating principle, namely hysteresis loss and eddy-current loss.
Moulding Machine
Metal injection molding (MIM) is a metalworking process in which finely-powdered metal is mixed with binder material to create a "feedstock" that is then shaped and solidified using injection molding. The molding process allows high volume, complex parts to be shaped in a single step.
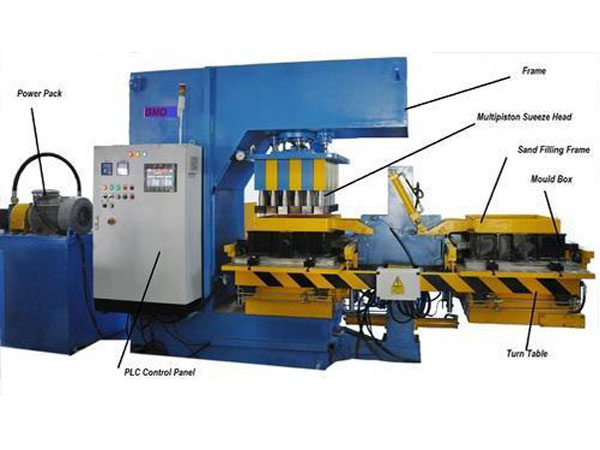
Address
23B, NS Road Kolkata
Contact
info@gleambusiness.com
+91-9681033767